By DON FLETCHER
News Staff Writer
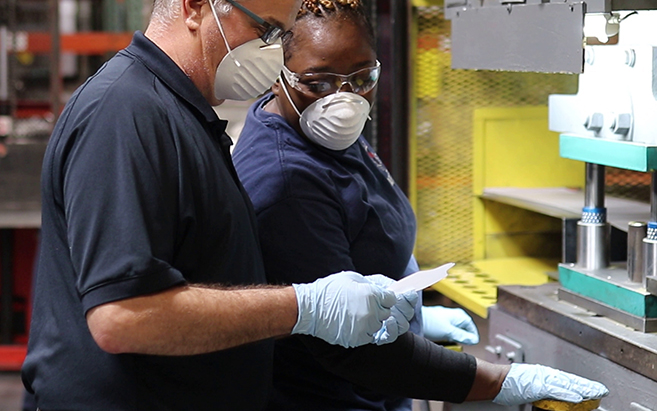
When the coronavirus pandemic began to filter into Escambia County, David Landa found a simple way to help. As the virus continued to spread through the area and the nation’s supply of personal protective equipment for healthcare workers began to diminish, Landa found a simple way to help.
Landa, president of Alto Products, began by buying 150 meals a week from local restaurants and having them delivered to hospital workers, doctors and other healthcare workers. Then other opportunities to help began popping up.
But, while doing what he could to help the community deal with the healthcare crisis, Landa also had to search for a way to keep Alto’s workforce working in the throes of a global economic crisis.
The plant’s current production plan will apparently help on both ends, at least for the time being.
“We’re still running three shifts a day, 24 hours a day, five days a week,” Landa said. “We’ve got almost 300 people working here, and business is slower than usual because of the pandemic. I had told the employees to use any vacation time they had saved up, just in case we had to cut back to four days a week.”
The company, which has manufactured automatic transmission parts in Atmore since 1995 and exclusively here since 1997, continued its three-shift production schedule, but the plant suddenly took on a different look.
“We initially set up three or four sewing machines …and put our people to work making disposable gowns, then we got more machines and started sewing those washable cotton masks,” he said. “We know how to make clutch plates, but we don’t know how to sew. So, we got some instructors in here to teach our people how to make them, and we borrowed a few more machines.
“The biggest problem with the masks and gowns is that you can’t make tens of thousands of them. We can make a few hundred at the time, probably not enough to fill the real need out there, so we are now making gowns and masks for our people to wear at work. It’s a help, just not a huge one.”
The company got a shot at possible mass fabrication of a piece of protective equipment that is currently gaining popularity with healthcare workers around the nation and globe, and the problem of job security was temporarily alleviated.
Through a multi-layered partnership, Alto was approached about production of a plastic face mask shield that will cut down on disposal of masks.
“This is an idea that could help not just our community, but the whole area and maybe the country,” Landa said. “What happened was, University of West Florida was partnering with the GE plant in Pensacola, making these plastic shields that fit over the N95 masks. They help save the masks so doctors or nurses can use them more than one time, and the shield is washable. The face shield is a good idea; I wish I had thought of it.”
Alto production managers and supervisors eagerly accepted the chance to produce the shields, which were then being made on a 3D printer at UWF.
“We very quickly built a tool to make the shields,” the company president said. “We can stamp those in our plant, and we’ve got the plastic. We can literally make thousands of those a day. Where we can do one a second, the 3D printer takes 30 minutes to an hour.”
Alto crews completed this week their first order, from Sacred Heart Hospital in Pensacola for 1,000 of the shields. Landa hopes that other facilities will follow suit for the duration of the COVID-19 pandemic and until national stockpiles are restored.
“We’re going to try and reach out to USA hospital and see if they have a need for them, or if there’s a need in our area,” he explained. “In Atmore (at Atmore Community Hospital) it’s less of an issue, because I don’t think they’re overrun with corona patients, and they don’t do a lot of heavy surgery there. If there are other hospitals around the area that might be short on mask shields, we can produce them very quickly.”
The future of the new Alto product line?
“We have talked with GE, and they’ve asked if we want to make this thing much bigger, so we’ll see,” said Landa. “We could probably make 100,000 of these in two or three weeks and get them out for basically nothing. In the long term, there won’t be a need (for Alto to produce the shields). Everybody will have enough masks, and everything will be OK. It’s probably peaking about now, and that’s fine with me.”
He added that all the steps taken by company officials in the midst of the COVID-19 crisis have been geared toward the betterment of the community.
“It’s not part of the business plan, for sure,” he joked about the PPE production. “But we really appreciate Atmore and everything Atmore has done for us. It’s been a great story. We started in 1995 with 12 employees; today, we have almost 300. I try not to forget where I come from. If there’s anything we can do to give back, we want to do it.”